bienhoa-Casting parts polishing is a kind of surface treatment process for casting parts, the purpose is to improve its appearance quality and finish, so that it can achieve a certain decorative effect and rust, corrosion, wear resistance and other performance requirements. In this paper, we will discuss the role of casting polishing, polishing principle, polishing process, polishing materials and equipment.
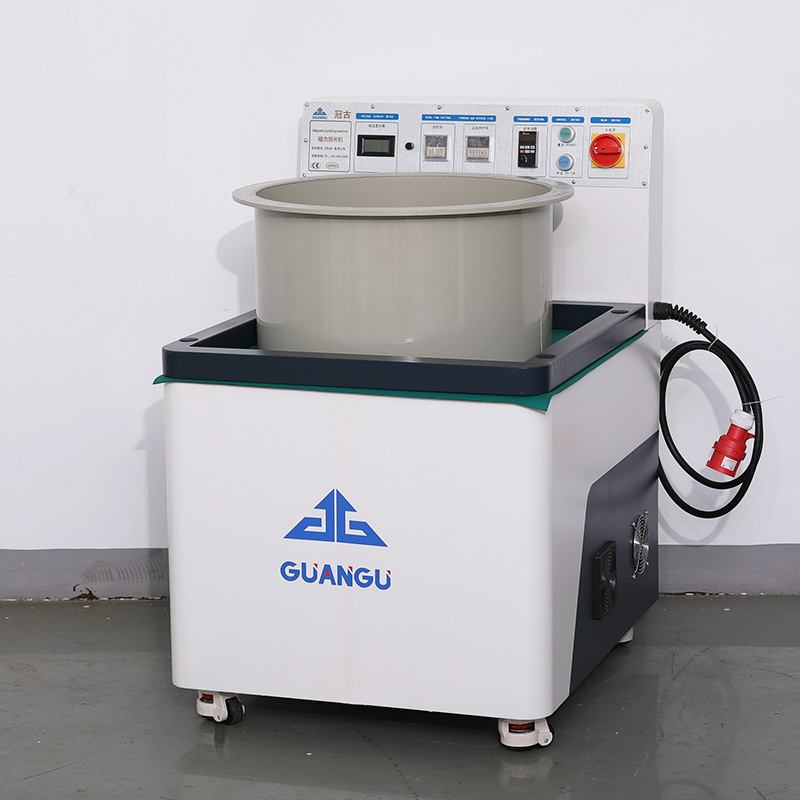
First, the role of casting polishing
- improve the quality of appearance: after polishing the casting surface finish is high, to meet the requirements of customers on the quality of product appearance, increase the ornamental and value of the product.
- Improve the anti-rust and anti-corrosion performance: the polishing process can make the tiny defects on the surface of the casting be repaired and improve the flatness of its surface, thus enhancing its anti-rust and anti-corrosion performance.
- Improve the wear-resisting performance: through polishing treatment, it can make the hardness distribution of the casting surface more uniform, improve its wear-resisting performance, and prolong the service life of the products.
- Improve assembly precision: Polishing treatment can make the surface precision of casting parts improve, which is conducive to improving the assembly precision of the product and reducing the assembly error.
Second, casting polishing principle
Casting parts polishing is mainly the use of abrasives on the surface of casting parts grinding, friction, to remove the surface of the microscopic defects, oxidation, rust and other impurities, so that the surface to achieve a flat, smooth effect. Polishing process, the abrasive, workpiece and polishing fluid interaction, realize the workpiece surface polishing treatment.
Third, casting polishing process
- Pre-polishing: Before formal polishing, the casting is pre-polished to remove the surface of the oxide skin, rust and other impurities, to create good conditions for subsequent polishing. Pre-polishing can be hand-polished or machine-polished.
- Rough polishing: use coarse abrasive polishing wheel to grind the surface of casting, remove the traces left by pre-polishing. In the rough polishing process, pay attention to control the polishing pressure to avoid scratching the surface of castings.
- medium polishing: on the basis of coarse polishing, use medium abrasive polishing wheel to polish, further refine the surface and improve the finish.
- fine polishing: using fine abrasive polishing wheel on the surface of the casting for fine polishing, so that the surface to achieve a higher degree of finish requirements. Fine polishing process, should be appropriate to reduce the polishing speed, reduce the polishing pressure, to avoid damage to the surface of the casting.
- Fine polishing: using finer abrasives and special polishing process, the surface of the casting is polished to a super high degree of finish. After fine polishing, the surface of castings can reach mirror effect.
Four, casting polishing materials and equipment
- Polishing materials: Polishing materials mainly include polishing wheel, polishing liquid and polishing belt. The material, hardness and particle size of polishing wheel have great influence on the polishing effect. Polishing liquid contains abrasives and additives, used to enhance the polishing effect.
- Polishing equipment: Polishing equipment includes polishing machines, polishing racks, conveyor belts and so on. Polishing machine has manual polishing machine, semi-automatic polishing machine and automatic polishing machine and other types, according to the production scale and polishing requirements to choose the appropriate equipment.
In short, casting polishing is an important surface treatment process, through the casting of polishing treatment, can improve its appearance quality, rust, corrosion and wear resistance. Mastering the correct polishing process and selecting suitable polishing materials and equipment is the key to realize the high quality polishing of castings.